تعمیر یا تعویض تجهیزات صنعتی؛ کدام مقرون به صرفه تر است؟
تصمیمگیری در مورد تعمیر یا تعویض تجهیزات صنعتی فرسوده یا از کار افتاده یکی از چالشهای اساسی پیش روی مدیران و مهندسان در صنایع مختلف است. این انتخاب تأثیر مستقیمی بر هزینههای عملیاتی بهرهوری کیفیت تولید و در نهایت سودآوری یک واحد صنعتی دارد. در این مقاله با رویکردی علمی و جامع به بررسی عوامل مؤثر در این تصمیمگیری و ارائه یک چارچوب تحلیلی برای انتخاب مقرونبهصرفهترین گزینه خواهیم پرداخت.
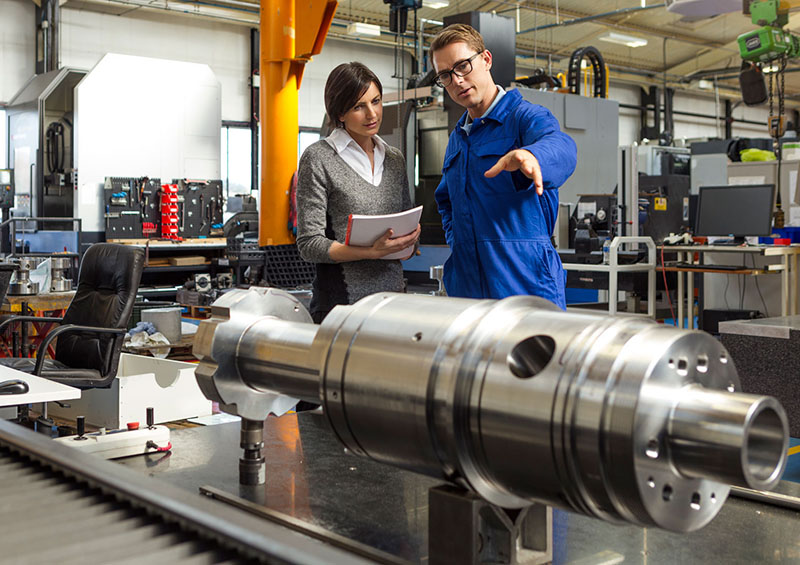
اهمیت تصمیمگیری صحیح در مورد تعمیر یا تعویض
انتخاب بین تعمیر و تعویض تجهیزات صنعتی تصمیمی استراتژیک است که پیامدهای بلندمدتی برای سازمان به همراه دارد. یک تصمیم نادرست میتواند منجر به افزایش هزینهها کاهش بهرهوری توقفهای مکرر تولید و حتی خطرات ایمنی شود. در مقابل یک انتخاب آگاهانه و مبتنی بر تحلیل دقیق میتواند به بهینهسازی هزینهها افزایش قابلیت اطمینان ماشین آلات صنعتی بهبود کیفیت محصولات و تضمین تداوم تولید کمک کند.
عوامل کلیدی در تصمیمگیری: تعمیر در مقابل تعویض
برای اتخاذ یک تصمیم منطقی و مقرونبهصرفه لازم است تا عوامل متعددی به دقت مورد ارزیابی قرار گیرند:
1. هزینه تعمیر در مقابل هزینه تعویض
اولین و بارزترین عامل در این تصمیمگیری مقایسه مستقیم هزینه تعمیر تجهیزات فعلی با هزینه خرید یک دستگاه جدید است. هزینه تعمیر شامل قطعات یدکی دستمزد تکنسینها زمان توقف تولید و سایر هزینههای جانبی مرتبط میشود. هزینه تعویض شامل قیمت خرید دستگاه جدید هزینههای نصب و راهاندازی و احتمالاً هزینههای برچیدن و دور انداختن دستگاه قدیمی است.
2. عمر مفید باقیمانده تجهیزات فعلی
ارزیابی دقیق عمر مفید باقیمانده تجهیزات فعلی نقش مهمی در این تصمیمگیری دارد. اگر تجهیزات پس از تعمیر نیز عمر کوتاهی داشته باشند و احتمال خرابیهای مکرر در آینده وجود داشته باشد تعویض ممکن است گزینه مقرونبهصرفهتری باشد. برای این ارزیابی باید سوابق تعمیر و نگهداری میزان استهلاک شرایط محیطی کارکرد و پیشبینیهای مربوط به خرابیهای آتی در نظر گرفته شوند.
3. هزینه فرصت ناشی از توقف تولید
توقف تولید برای انجام تعمیرات هزینههای قابل توجهی را به سازمان تحمیل میکند. این هزینهها شامل از دست رفتن تولید تأخیر در تحویل سفارشات جریمههای قراردادی و استفاده غیربهینه از نیروی کار میشود. اگر تعمیرات زمانبر باشند و منجر به توقف طولانی مدت تولید شوند هزینه فرصت میتواند به مراتب بیشتر از هزینه خود تعمیرات باشد و در این صورت تعویض سریعتر تجهیزات ممکن است اقتصادیتر باشد.
4. بهرهوری و کارایی تجهیزات جدید در مقابل تجهیزات تعمیرشده
تجهیزات جدید معمولاً از فناوریهای پیشرفتهتری بهره میبرند و کارایی و بهرهوری بالاتری دارند. این امر میتواند منجر به کاهش مصرف انرژی افزایش سرعت تولید بهبود کیفیت محصولات و کاهش ضایعات شود. مقایسه بهرهوری تجهیزات جدید با تجهیزات تعمیرشده (که ممکن است همچنان کارایی پایینتری داشته باشند) در بلندمدت میتواند نشان دهد که آیا سرمایهگذاری در یک دستگاه جدید بازگشت سرمایه بیشتری را به همراه خواهد داشت یا خیر.
5. هزینه نگهداری و تعمیرات آتی
تجهیزات قدیمیتر معمولاً نیاز به نگهداری و تعمیرات بیشتری دارند. با تعویض یک دستگاه فرسوده با یک دستگاه جدید هزینههای نگهداری و تعمیرات آتی به طور قابل توجهی کاهش مییابد. برآورد هزینههای نگهداری پیشبینیشده برای تجهیزات فعلی پس از تعمیر در مقابل هزینههای نگهداری یک دستگاه جدید در طول عمر مفید آن یک عامل مهم در تصمیمگیری است.
6. در دسترس بودن قطعات یدکی و سهولت تعمیر
برای تجهیزات قدیمیتر یافتن قطعات یدکی ممکن است دشوار و پرهزینه باشد و تعمیرات پیچیدهتر و زمانبرتر شوند. در مقابل تجهیزات جدید معمولاً از قطعات یدکی فراوانتری برخوردارند و تعمیرات آنها ممکن است سادهتر و سریعتر انجام شود. این عامل میتواند به طور قابل توجهی بر هزینههای نگهداری و زمان توقف تولید تأثیر بگذارد.
7. ایمنی و مسائل زیستمحیطی
تجهیزات قدیمی ممکن است استانداردهای ایمنی و زیستمحیطی فعلی را رعایت نکنند. تعمیر این تجهیزات برای انطباق با استانداردها میتواند پرهزینه باشد. تعویض با یک دستگاه جدید که مطابق با آخرین استانداردهای ایمنی و زیستمحیطی طراحی شده است میتواند خطرات احتمالی را کاهش داده و از بروز مشکلات قانونی جلوگیری کند.
8. پیشرفتهای فناوری و نوآوری
در برخی موارد پیشرفتهای فناوری منجر به تولید تجهیزات جدیدی با قابلیتها و عملکردهای بسیار بهتر شده است. تعویض تجهیزات قدیمی با دستگاههای جدید میتواند فرصتهای جدیدی برای بهبود فرآیندهای تولید افزایش کیفیت محصولات و کاهش هزینهها از طریق اتوماسیون و سایر فناوریهای نوین فراهم کند.
9. ارزش اسقاط تجهیزات قدیمی
ارزش اسقاط تجهیزات قدیمی نیز باید در محاسبات مربوط به تعویض در نظر گرفته شود. فروش قطعات قابل استفاده یا بازیافت مواد میتواند بخشی از هزینه خرید دستگاه جدید را جبران کند.
10. ملاحظات مالی و بودجهای
محدودیتهای بودجهای سازمان نیز یک عامل مهم در تصمیمگیری است. حتی اگر تعویض تجهیزات در بلندمدت مقرونبهصرفهتر باشد ممکن است سازمان در حال حاضر منابع مالی کافی برای خرید یک دستگاه جدید را نداشته باشد و مجبور به انتخاب گزینه تعمیر شود.
چارچوب تحلیلی برای تصمیمگیری: روشهای ارزیابی اقتصادی
برای اتخاذ یک تصمیم آگاهانه و مبتنی بر دادهها میتوان از روشهای مختلف ارزیابی اقتصادی استفاده کرد:
1. تحلیل هزینه-فایده (Cost-Benefit Analysis)
در این روش تمام هزینهها و مزایای مرتبط با هر دو گزینه (تعمیر و تعویض) در طول عمر مفید پیشبینیشده مورد ارزیابی قرار میگیرند. هزینهها شامل هزینه تعمیر/تعویض هزینههای نگهداری آتی هزینه توقف تولید و هزینههای انرژی میشوند. مزایا شامل افزایش بهرهوری بهبود کیفیت کاهش ضایعات افزایش ایمنی و ارزش اسقاط. با مقایسه خالص مزایا (مزایا منهای هزینهها) برای هر گزینه میتوان تصمیم بهتری اتخاذ کرد.
2. محاسبه نرخ بازگشت سرمایه (Return on Investment – ROI)
برای گزینه تعویض میتوان نرخ بازگشت سرمایه را با در نظر گرفتن صرفهجوییهای ناشی از افزایش بهرهوری کاهش هزینههای نگهداری و سایر مزایا در طول عمر مفید دستگاه جدید محاسبه کرد. اگر نرخ بازگشت سرمایه بالاتر از نرخ مورد انتظار سازمان باشد تعویض میتواند یک سرمایهگذاری جذاب محسوب شود.
3. تحلیل نقطه سربه سر (Break-Even Analysis)
این روش به تعیین نقطهای کمک میکند که در آن هزینههای تعمیر با هزینههای تعویض برابر میشوند. با پیشبینی هزینهها و مزایای هر دو گزینه در طول زمان میتوان تعیین کرد که پس از چه مدتی مزایای ناشی از تعویض (مانند کاهش هزینههای عملیاتی) از هزینه اولیه آن پیشی میگیرد.
4. ارزش فعلی خالص (Net Present Value – NPV)
در این روش تمام جریانهای نقدی مرتبط با هر دو گزینه (هزینهها و درآمدها) در طول عمر مفید پیشبینیشده به ارزش فعلی تبدیل میشوند. گزینهای که دارای ارزش فعلی خالص بالاتری باشد از نظر اقتصادی جذابتر است. این روش ارزش زمانی پول را نیز در نظر میگیرد.
5. دوره بازگشت سرمایه (Payback Period)
این روش مدت زمانی را نشان میدهد که طول میکشد تا صرفهجوییهای ناشی از تعویض تجهیزات هزینه اولیه خرید آن را جبران کند. دوره بازگشت سرمایه کوتاهتر معمولاً جذابتر است اما باید در کنار سایر روشهای ارزیابی مورد توجه قرار گیرد.
فرآیند تصمیمگیری گام به گام
یک فرآیند ساختاریافته برای تصمیمگیری در مورد تعمیر یا تعویض تجهیزات صنعتی میتواند به شرح زیر باشد:
- شناسایی مشکل و جمعآوری اطلاعات: تعیین دقیق مشکل یا دلیل از کار افتادگی تجهیزات جمعآوری سوابق تعمیر و نگهداری اطلاعات مربوط به عملکرد فعلی و هزینههای جاری.
- ارزیابی وضعیت فنی: انجام بازرسیهای دقیق برای تعیین میزان آسیب دیدگی عمر مفید باقیمانده و امکانپذیری تعمیر.
- برآورد هزینهها: تخمین دقیق هزینههای تعمیر (شامل قطعات دستمزد زمان توقف) و هزینههای تعویض (شامل قیمت خرید نصب برچیدن دستگاه قدیمی).
- تحلیل مزایا و معایب: شناسایی و ارزیابی مزایا و معایب هر دو گزینه (بهرهوری کیفیت ایمنی مسائل زیستمحیطی).
- انجام ارزیابی اقتصادی: استفاده از روشهای تحلیل هزینه-فایده ROI NPV و سایر روشهای مناسب برای مقایسه اقتصادی گزینهها.
- در نظر گرفتن عوامل کیفی: علاوه بر عوامل اقتصادی عوامل کیفی مانند تأثیر بر روحیه کارکنان تصویر برند و ریسکهای عملیاتی نیز باید در نظر گرفته شوند.
- تصمیمگیری: بر اساس تحلیلهای انجام شده و با در نظر گرفتن تمام عوامل مؤثر تصمیم نهایی در مورد تعمیر یا تعویض اتخاذ شود.
- اجرای تصمیم: اقدام به تعمیر تجهیزات یا خرید و نصب دستگاه جدید.
- پیگیری و ارزیابی نتایج: پس از اجرای تصمیم نتایج (مانند هزینههای واقعی بهرهوری و قابلیت اطمینان) باید پیگیری و با پیشبینیها مقایسه شوند تا درسهای لازم برای تصمیمگیریهای آتی گرفته شود.
نقش فناوری در مدیریت نگهداری و تعمیرات
پیشرفتهای فناوری ابزارهای قدرتمندی را برای مدیریت نگهداری و تعمیرات در اختیار سازمانها قرار داده است. سیستمهای مدیریت داراییهای سازمانی (EAM) و سیستمهای مدیریت نگهداری مکانیزه (CMMS) میتوانند به جمعآوری و تحلیل دادههای مربوط به عملکرد تجهیزات سوابق تعمیر و نگهداری هزینهها و پیشبینی خرابیها کمک کنند. استفاده از این سیستمها میتواند فرآیند تصمیمگیری در مورد تعمیر یا تعویض را بهبود بخشیده و مبتنی بر دادههای دقیقتر کند.
نتیجهگیری
تصمیمگیری در مورد تعمیر یا تعویض تجهیزات صنعتی یک فرآیند پیچیده است که نیازمند تحلیل دقیق عوامل فنی اقتصادی و کیفی است. هیچ پاسخ قطعی و یکسانی برای همه شرایط وجود ندارد و بهترین گزینه به عوامل متعددی از جمله وضعیت فعلی تجهیزات هزینهها بهرهوری عمر مفید باقیمانده و اهداف استراتژیک سازمان بستگی دارد. با استفاده از یک چارچوب تحلیلی جامع و بهرهگیری از ابزارهای مدیریت نگهداری مدرن مدیران و مهندسان میتوانند تصمیمات آگاهانهتری اتخاذ کرده و منابع سازمان را به طور بهینه مدیریت کنند. در نهایت هدف یافتن مقرونبهصرفهترین راهکار برای حفظ عملکرد پایدار و کارآمد مواد اولیه صنعتی و فرآیندهای تولید است.
آیا شما به دنبال کسب اطلاعات بیشتر در مورد "تعمیر یا تعویض تجهیزات صنعتی؛ کدام مقرون به صرفه تر است؟" هستید؟ با کلیک بر روی اقتصادی, کسب و کار ایرانی، به دنبال مطالب مرتبط با این موضوع هستید؟ با کلیک بر روی دسته بندی های مرتبط، محتواهای دیگری را کشف کنید. همچنین، ممکن است در این دسته بندی، سریال ها، فیلم ها، کتاب ها و مقالات مفیدی نیز برای شما قرار داشته باشند. بنابراین، همین حالا برای کشف دنیای جذاب و گسترده ی محتواهای مرتبط با "تعمیر یا تعویض تجهیزات صنعتی؛ کدام مقرون به صرفه تر است؟"، کلیک کنید.